The no-load performance of the five-stage laminated core transformer, Shang Yafei (Xinjiang Special Transformer Co., Ltd. Transformer Factory, Changji 830, Xinjiang) analyzed the mechanism of the five-stage joint core to reduce the no-load loss, no-load current and noise, and pointed out the core. The use of a five-stage seam core structure can greatly improve the no-load performance of the transformer.
1 Introduction Energy saving and consumption reduction is a development direction of transformers, and reducing the no-load loss by improving the core lamination structure is a major way to reduce transformer losses. In some developed countries, transformer factories generally use five-stage joint core technology, which has significantly improved the no-load performance of the core compared with the traditional secondary joints in China. The TUG M H800×5 000 automatic core cross-cutting line of German Georg Company introduced in the technical transformation of our factory in 1998 is used for processing silicon steel sheets. The maximum length of shear can be processed by three angles of ±45°. It can automatically cut three, five and seven seam silicon steel sheets. After adopting the five-stage joint core structure, the no-load performance of our products, such as no-load loss and no-load current, has dropped significantly, and the noise level has also been reduced to some extent. Especially on large-capacity products, the effect is more obvious. This paper briefly introduces the structural form of the five-level seam core, the mechanism of reducing consumption and the energy-saving effect of the product.
2 Five-level joint core structure and characteristics We know that the no-load loss of the transformer is mainly composed of basic loss, joint loss and shear edge loss. In addition to the basic loss, the seam loss accounts for a large proportion and the shear edge loss is small. Seam loss is a magnetic flux density that is closely related to the local flux density, especially the seam area. Due to the influence of the joint gap, the local magnetic density increases, resulting in an increase in local loss of the core. Therefore, reducing this effect is also an effective way to reduce losses.
At present, the domestic transformer manufacturer iron core generally adopts two or three-level joint laminations, the iron core laminations are staggered according to a certain distance, and two parallel joints are formed in the staggered area, and the magnetic flux distribution at the joint of the iron core is as shown in Fig. 1. As shown, the thin solid line in the figure is a magnetic field line, and the dotted line is a half magnetic field line.
Two of the corresponding seams span a stack of sheets. Since the magnetic reluctance of the air is several thousand times higher than the magnetic resistance of the silicon steel sheet, most of the magnetic flux in the lamination passes through the bridging laminations. In addition, the magnetic flux passes through the 45° angle joint. Since the area of ​​the joint is twice the cross-sectional area of ​​the core column, the magnetic density of the joint area is 22 times that of the core column. However, at the end of the two seamed silicon steel sheets, most of the magnetic flux passes through a layer of bridging laminations, and the layer is magnetically dense across the end of the lamination: where the magnetic density in the B-pillar is as shown in FIG. A three-stage seam core in which two corresponding seam gaps span two laminates, and the magnetic flux at the end of the three seam silicon steel sheets passes through the two layers of the cross-over lamination, each layer spanning the end of the lamination The magnetic density is: the transformer and so on, the relationship between the local magnetic flux density B and the number of joints N is: due to the loss of the joint area in the core and the approximate relationship between the no-load current and the magnetic density B can be written as silicon steel sheet And frequency related constants. Substituting equation (3) into equations (4) and (5), the approximate relationship between local loss and no-load current in the joint area and the number N of core joints can be obtained: for example, the working magnetic density of the transformer is 1 .75T, from the formula (1), the magnetic density in the joint spanning lamination is 2.47T. The magnetic density of the cold-rolled silicon steel sheet used in the transformer is already saturated, which results in a saturation of 1.9~1.92T. The no-load loss and no-load current in the seam area increase sharply.
It can be seen from equations (6) and (7) that as the number of joints of the core increases, the no-load loss and no-load current in the joint area of ​​the core gradually decrease, but the local loss and the magnitude of the no-load current decrease. Will be getting smaller and smaller.
However, the number of laminated sheets increases with the number of lamination stages, and the production efficiency of silicon steel sheet shearing and core lamination is reduced. This contradiction is only through advanced silicon steel sheet shearing equipment and advanced lamination process. And choose the appropriate seam level to solve. After nearly two years of production practice, we believe that kV-class transformers are more suitable for single-piece stacking of five-stage joints. The production efficiency is higher than that of ordinary secondary or tertiary joints, which can fully meet the needs of production. Now compare the difference between the local loss and the no-load current of the five-level joint and the third-level joint.
According to formula (4) and formula (5), the five-level joint (working magnetic density ordinary three-level joint: the local loss of the five-level joint core and the percentage of the no-load current reduction of the third-order seam core) For: the no-load loss of the transformer can be written as P = K. P depends on the core material, magnetic density and frequency unit loss, W kg core weight, kg depends on the structural form of the core and the additional factor of the manufacturing process level for cold rolling For silicon steel sheets, the K value is generally taken from 1.1 to 1.2. The smaller the core diameter is, the larger the value is. For the kV grade product, the total is 1.12.
According to the calculation result of equation (12), the additional coefficient of no-load loss should be about 1.08, but since the stack of iron cores of our factory adopts a stack, effectively reducing the eddy current loss in the local area, plus the core sheet shearing. The burrs are very small, making the core joints smaller, so the additional factor of no-load loss is generally around 1.05, and has been verified in multiple products. It can be seen from the above that the no-load loss of the five-stage seam core is reduced by 5 to 8 on average, and the no-load current is reduced by more than 30. The energy-saving effect is very remarkable.
3 Other characteristics of the five-level seam core Compared with the traditional two-stage or three-stage joint, the five-stage seam core lamination has the following characteristics in addition to the large reduction of no-load loss and no-load current.
3.1 Noise The noise of the transformer is mainly due to the magnetostriction of the silicon steel sheet, but the magnetic attraction between the silicon steel sheet joint and the lamination is also one of the causes of noise. The amount of noise depends on the length of the seam gap and the size of the magnetic density. According to the relevant data, the magnetic field energy differential form of the joint air gap is: the magnetic flux density in the joint gap of B, the magnetic permeability in T air, and the mechanical work dA = FdL of H m magnetic field energy. B thus obtains the joint area of ​​the S core in the magnetic attraction type, m thus causes the elastic modulus of the E silicon steel sheet in the lamination elongation strain type according to the study of the sinking, and the corresponding sound intensity level in the L core stack The length of the joint gap, cm assumes that the working magnetic density of the transformer is 1.7T, the length of the three-level joint gap is 0.05 cm, and the three-level joint gap magnetic density is about 0.4 ton, which is visible from the transformer, and the five-level joint The iron core is reduced by about 3dB compared with the ordinary three-stage seam core. For the traditional two-stage and three-level joint laminations, the air gap of a certain section of the joint is concentrated, and a large alternating electromagnetic force acts on the core, causing Strong vibrating sound However, in the five-level seam core, the joint air gap of a section in the joint area is greatly reduced, the magnetic line can smoothly enter the adjacent laminations, and the no-load current is also greatly reduced. The electromagnetic force on the yoke is small, and the electromagnetic force in the joint area The laminate is pressed so that the noise of the transformer is significantly reduced.
3.2 High production efficiency At present, many domestic transformer manufacturers reduce the no-load loss and noise. Usually, the core adopts a stack of three-stage seam laminated structure. Due to the limitation of the silicon steel sheet cross-cutting equipment, the total number of times of core shearing of a single transformer is increased, and the iron core stacking man-hours are also prolonged, resulting in a decrease in production efficiency. Our factory adopts the latest core cross-cutting equipment, which greatly improves the shearing efficiency of the core, and can achieve up to seven-stage single-piece stack seams. Considering the technicality of core stacking and inserting, our factory adopts five-stage single-piece laminated seam structure. The core piece has a 定ä½20 positioning hole, and the iron core can be directly loaded with the code, and the production efficiency is greatly improved.
3.3 Saving materials Due to the use of advanced core cross-cutting equipment, the shear burr of silicon steel sheet is less than 0.03mm, coupled with the high quality of the workers, the stacking deviation of the core is less than 2mm, and the joint gap is very small. The optimized design of the core section makes the set gap of the transformer winding to the core of our factory reduced from the original 5mm to the current 2.5mm, and the electromagnetic wire usage of the transformer can be reduced. Since our factory produces about 100 transformers of kV and above every year, its material saving effect is very considerable.
4 Transformer no-load performance comparison Compare the measured values ​​of six kV-class transformers (three of which use three-stage joint laminations and three of single-piece lamination five-level joints), and the specific no-load performance values.
Model noise dB Note: I is a five-level seam core II is a three-stage seam core (working magnetic density is about 1.7T). It can be seen from Table 1 that the five-level seam core has an average no-load loss compared to the three-stage seam core. Decreased by 8, the no-load current dropped by an average of 50, and the noise dropped by an average of 4 dB.
5 Conclusion In summary, the five-level seam core has the advantages of low loss, low noise and good processability. Its adoption plays a role in saving energy, improving power supply quality and reducing noise pollution to the environment. In particular, the iron core of our factory adopts the process of not stacking the iron yoke, which reduces the damage to the silicon steel sheet, and the no-load loss can be reduced by about 2. After nearly two years of production practice, the no-load loss of our factory kV grade products has dropped by more than 8 on average, the no-load current has dropped by more than 30, and the noise has dropped by an average of 4 dB. It can be said that with the current core material, the no-load performance of the transformer should be improved. The use of a five-level seam laminate structure is undoubtedly the best production method, and is also an ideal structural form to replace the traditional two-stage, three-level seam laminated core.
ZGAR Vape Pods 1.0
ZGAR Vape Pods 1.0
ZGAR electronic cigarette uses high-tech R&D, food grade disposable pods and high-quality raw material. A new design of gradient our disposable vape is impressive.We equip with breathing lights in the vape pen and pods.
Our team has very high requirements for product quality, taste allocation and packaging design. Designers only use Hong Kong designers, e-cigarette liquid only imports from the United States, materials are food grade, and assembly factory wants medical grade without ground workshop.
We offer best price, high quality Pod System Vape,Pods Systems Touch Screen,Empty Pod System, Pod Vape System,Disposable Pod device,Vape Pods to all over the world.
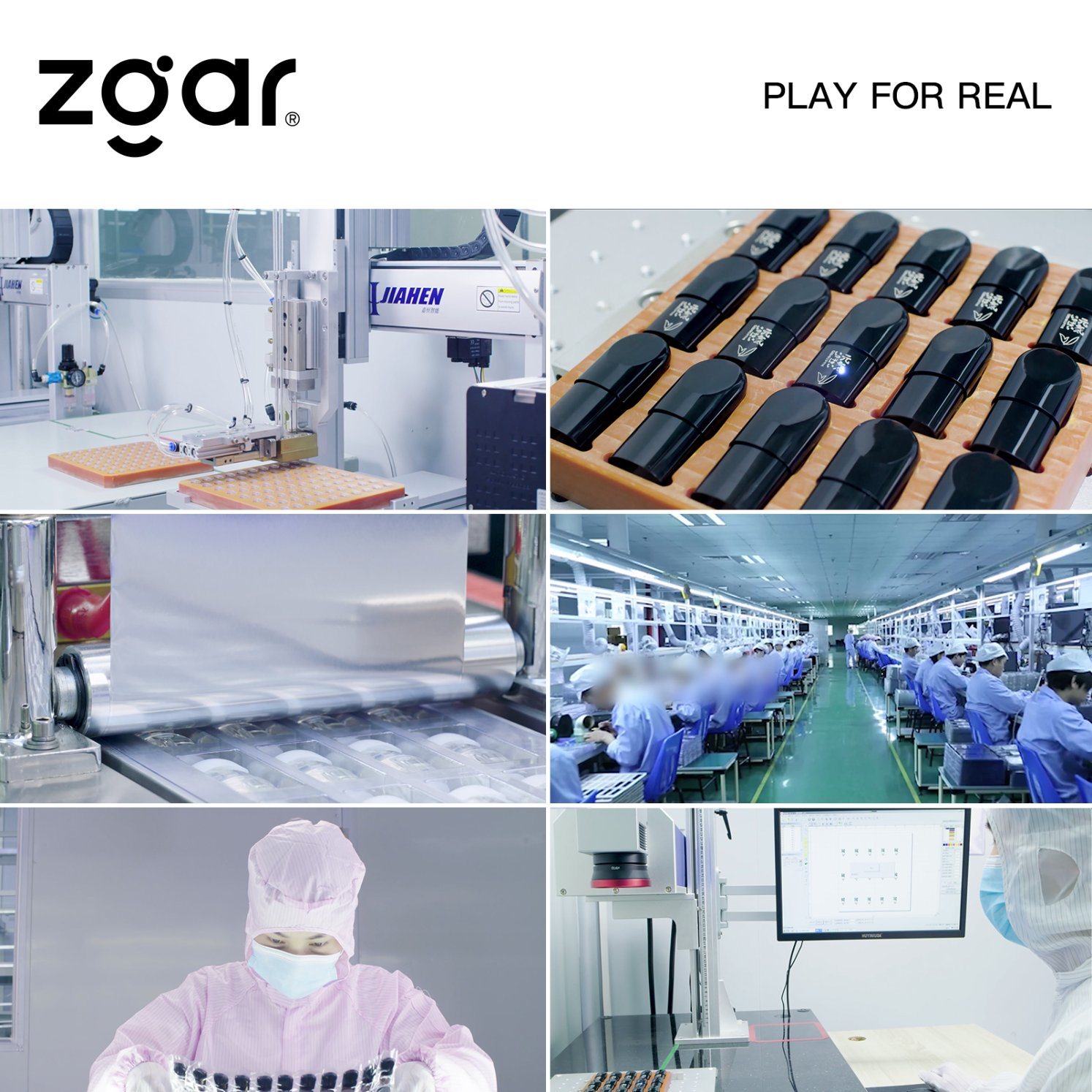
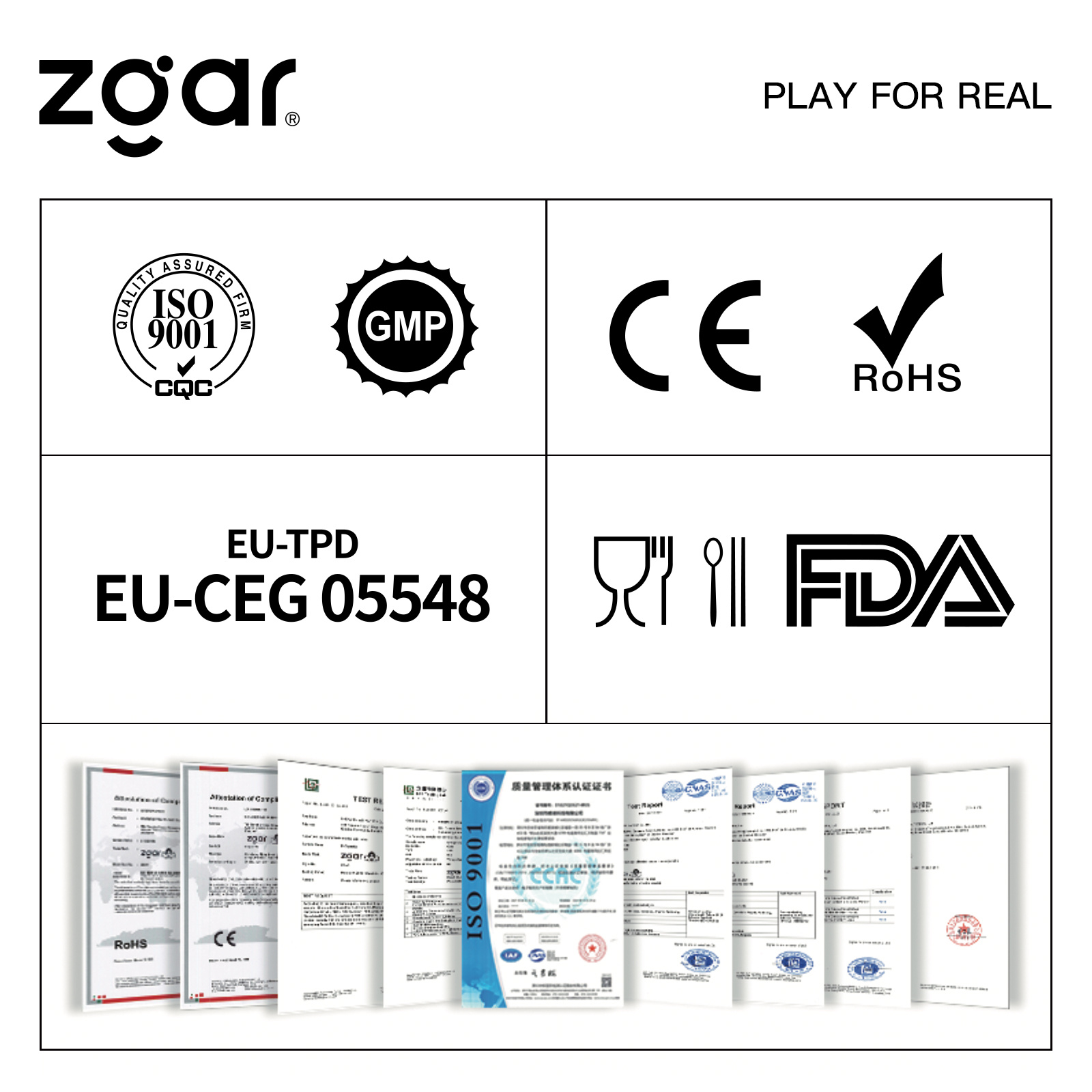
Pods,Vape Pods,Pod Systems,Atomizer, E-cigarette, Empty Pod Vape Manufacturer and Supplier in China
ZGAR INTERNATIONAL TRADING CO., LTD. , https://www.szdisposable-vape.com